The Brain of UAV Motion: Next-Gen IMUs
Many industries incorporate IMU (Inertial Measurement Unit) sensors for operations requiring navigation, stabilization, tracking, or positioning for various operations. An IMU is a sensor that helps the integrated devices track their movement and orientation. IMUs achieve this by measuring acceleration, rotation, and sometimes magnetic fields to understand how something moves in space.
Aircraft are one of the many usage areas of IMU sensors that require the highest technology to ensure the utmost safety. Considered the brain of the aircraft, electronic navigation systems are responsible for collecting and providing all flight information so that the pilot can focus on monitoring. In the past, a magnetic compass and a map were used for aircraft navigation. A technique called dead-reckoning was used to estimate the aircraft’s position based on its last known location, speed, direction, and time traveled. Thanks to advanced technologies, pilots can master and use more reliable navigation systems.
A UAV’s navigation system combines multiple sensors and technologies to enable stable flight and autonomous operations. An IMU within a UAV is typically located on the flight controller board which is positioned close to the center of mass. The center of mass is the point where the UAV’s weight is evenly distributed in all directions. Placing the IMU here helps ensure:
Accurate motion detection: Measuring angular changes (pitch, roll, yaw) without extra distortions. Hence the system receives more consistent and reliable motion data.
Minimized vibrations and noise: Due to their sensitivity to motion, they are mounted on dampening materials to reduce the vibrations from propellers and motors.
Reduced drift errors: Placed anywhere too far from the center, slight movements could be exaggerated. An IMU near the center can accurately measure orientation changes and minimize the effects of drift. This improves the dead reckoning system, allowing the UAV to estimate its position without GPS by relying solely on the data from its IMU.
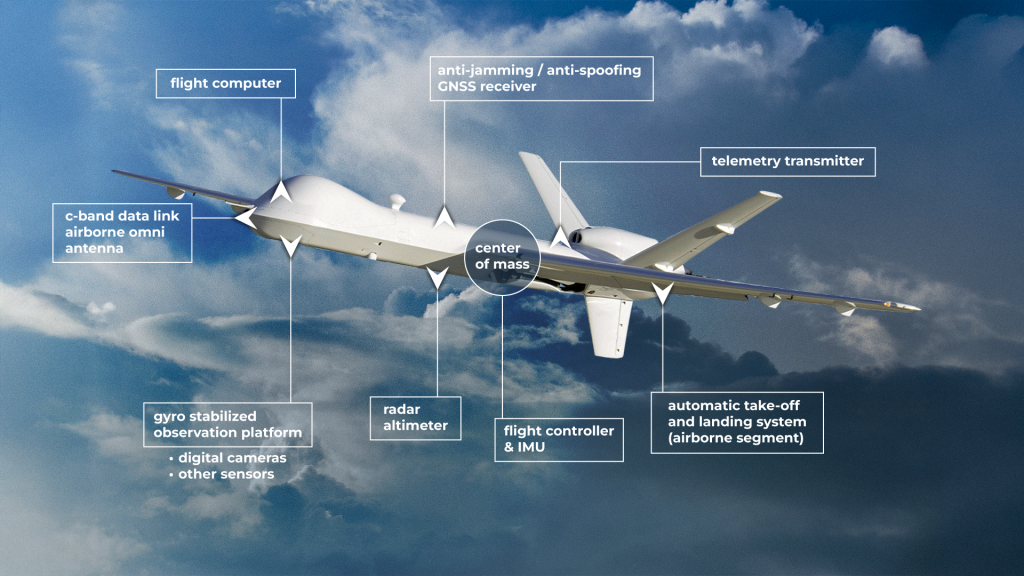
With modern technological breakthroughs, IMUs are smaller, lighter, more accurate, process data faster, more durable, and consume less power. These improvements allow them to be more versatile, efficient, and reliable overall. Advanced IMUs are a perfect fit for long-duration flights even in harsh weather conditions with unceasing autonomous navigation and precision maneuvers.
Safran Sensing Technologies Norway designs and manufactures high-accuracy IMU solutions that hold the industry’s best SWaP (size, weight, and power consumption) to cost ratio. In addition to UAVs and target drones, their gyro and IMU modules can be used in a variety of applications including; mapping, DIRCM (Directed Infrared Countermeasure) systems, AHRS, navigation & guidance, defence systems, and Radar (platform)/LIDAR/image stabilization.
Safran Sensing Technologies’ lightweight and small form factors with low power consumption and shock resistance improve UAVs’ performance and integrity during flight, take-off, and landing, and in case of emergencies.
This reliability is crucial for UAVs in defence, surveillance, and industrial inspections, where consistent performance is essential. Safran’s IMU sensors ensure precise navigation and stability, even in high-vibration or high-G environments, minimizing system failure risks. Their robust design enhances mission success by providing real-time, accurate data, enabling confident decision-making in harsh or dynamic conditions.
For more information on Safran Sensing Technologies Norway:
Contact us for Safran solutions: